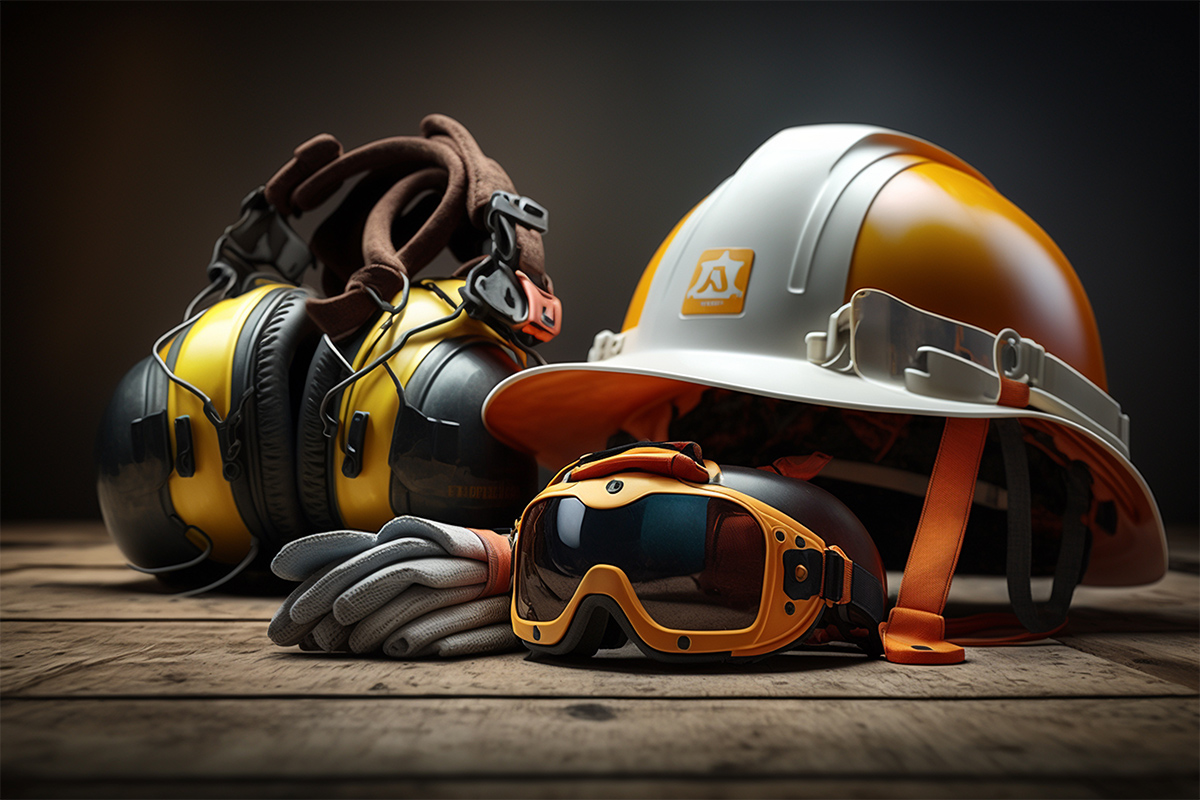
In industrial environments, the safety of workers is paramount. Safety equipment plays a vital role in preventing accidents, minimizing injuries, and ensuring that employees are protected from potential hazards. Whether you’re operating in the construction, manufacturing, or oil and gas sector, safety equipment is essential for safeguarding workers in potentially dangerous environments. Proper safety measures not only protect workers but also ensure that businesses comply with regulations, reduce liability, and increase productivity by preventing workplace accidents.
The Importance of Safety Equipment
Safety equipment is designed to protect workers from various risks such as falls, exposure to hazardous materials, electrical shocks, and mechanical injuries. Whether it’s personal protective equipment (PPE) like helmets, gloves, and goggles, or safety systems like fire extinguishers, gas detectors, and emergency alarms, the right safety equipment minimizes the risk of injury and ensures that workers can perform their duties without unnecessary danger.
In sectors like construction and oil and gas, workers often face heightened risks due to the nature of the tasks they are performing. For example, construction workers may be exposed to falling debris, heavy machinery, and hazardous chemicals. In such environments, safety equipment, such as hard hats, high-visibility vests, and safety boots, plays a critical role in reducing the likelihood of accidents.
Types of Safety Equipment
There are various types of safety equipment, each designed to protect workers from specific hazards. Some of the most common types include:
-
Personal Protective Equipment (PPE): PPE includes items such as helmets, goggles, gloves, safety boots, and ear protection. These are essential for workers who are exposed to physical, chemical, or biological hazards. For example, hard hats protect workers from head injuries caused by falling objects, while ear protection safeguards against hearing damage from loud machinery.
-
Fall Protection Equipment: In industries like construction, where workers frequently work at heights, fall protection equipment is a must. This includes harnesses, lanyards, and safety nets that prevent falls or minimize the impact of a fall. These are critical for ensuring worker safety on elevated surfaces like scaffolding, ladders, and rooftops.
-
Fire Safety Equipment: Fires can occur in any industrial setting, and having the right fire safety equipment is essential. Fire extinguishers, fire blankets, and fire hoses are commonly used to put out small fires before they become hazardous. Additionally, fire-resistant clothing and emergency escape routes ensure workers can act quickly in the event of a fire.
-
Respiratory Protection: Workers in environments with airborne hazards, such as chemicals, fumes, dust, or smoke, require respiratory protection. This includes masks, respirators, and air-purifying devices designed to filter out harmful particles. For example, workers in construction or demolition may use respirators to protect against inhaling dust or asbestos fibers.
-
Safety Signage and Barriers: Safety signs and barriers are crucial for alerting workers to potential hazards. They help create a safer work environment by indicating the presence of dangers such as electrical hazards, toxic chemicals, or high-voltage equipment. Properly placed signage can help prevent accidents by providing important warnings and instructions.
How Safety Equipment Protects Workers
Safety equipment protects workers in several ways, depending on the type of hazard present in the work environment. For example, fall protection equipment prevents serious injury or death by stopping workers from falling from heights. Similarly, fire safety equipment helps to control fires and prevent them from spreading, minimizing potential damage and injury.
Respirators and masks are designed to protect workers from harmful chemicals or airborne particles. In environments where workers are exposed to hazardous materials, such as factories or construction sites, respiratory protection is essential to prevent long-term health issues such as lung disease or chemical poisoning.
Additionally, personal protective equipment (PPE) such as gloves, safety boots, and helmets acts as a first line of defense against physical injuries. For instance, safety boots protect workers from stepping on sharp objects or from being crushed by heavy equipment. Protective gloves help prevent cuts and abrasions when handling sharp tools or materials.
Safety Regulations and Compliance
In most industries, safety equipment is not optional; it is a legal requirement. Regulatory bodies such as OSHA (Occupational Safety and Health Administration) in the United States and similar organizations worldwide set strict safety standards that employers must follow. These regulations require businesses to provide workers with the necessary safety equipment to prevent accidents and ensure safe working conditions.
Non-compliance with safety regulations can result in severe consequences for businesses, including fines, legal action, and damage to the company’s reputation. In some cases, failure to provide adequate safety equipment can even lead to worker fatalities. By investing in high-quality safety equipment and adhering to safety standards, companies can protect their employees and avoid costly legal issues.
Choosing the Right Safety Equipment
Choosing the right safety equipment requires a thorough understanding of the specific risks associated with the work environment. Businesses should assess the potential hazards their workers may encounter and select equipment that effectively addresses these risks. For example, workers exposed to loud machinery should be provided with ear protection, while those working with chemicals should have access to gloves and respiratory protection.
It’s also important to consider the comfort and fit of safety equipment. Workers are more likely to wear safety gear if it is comfortable and well-fitted. Ill-fitting helmets, gloves, or boots can be distracting and may not provide the intended protection, so proper sizing and comfort should be prioritized.
Conclusion
Safety equipment is a critical investment for any business operating in high-risk industries. It not only protects workers from potential harm but also ensures compliance with safety regulations and boosts productivity by reducing accidents and downtime. By providing the right safety gear and fostering a safety-conscious culture, companies can create a secure work environment and demonstrate their commitment to their employees’ well-being.